The impeller design is a critical factor that directly affects a slurry pump’s ability to handle highly abrasive or corrosive slurries, both in terms of operational efficiency and service life. The impeller is the core component responsible for imparting kinetic energy to the slurry and is the part most exposed to wear and chemical attack. Several design elements work together to determine how well an impeller can manage harsh slurry conditions:
1. Material Composition
The choice of material is the first line of defense against wear and corrosion. For highly abrasive slurries, impellers are often made from high-chromium white iron, which provides excellent hardness and erosion resistance. In corrosive environments, materials such as rubber, polyurethane, stainless steel, or specialty alloys (e.g., duplex stainless steels or Hastelloy) are preferred for their chemical stability. Some applications may even use ceramic coatings or composite materials to enhance durability.
2. Impeller Type
Open and Semi-Open Impellers: These designs are better suited for handling slurries with large or irregular solids, as they are less prone to clogging and allow easier passage. Their open structure, however, can make them more vulnerable to high wear unless adequately reinforced.
Closed Impellers: Offer higher efficiency by minimizing internal recirculation and leakage, but are more sensitive to wear in highly abrasive slurries, especially when clearances between impeller and casing cannot be maintained.
Vortex (Recessed) Impellers: These create a vortex that pulls the slurry through the pump with minimal direct contact between the solids and the impeller. This design greatly reduces wear and is ideal for fragile or very abrasive solids.
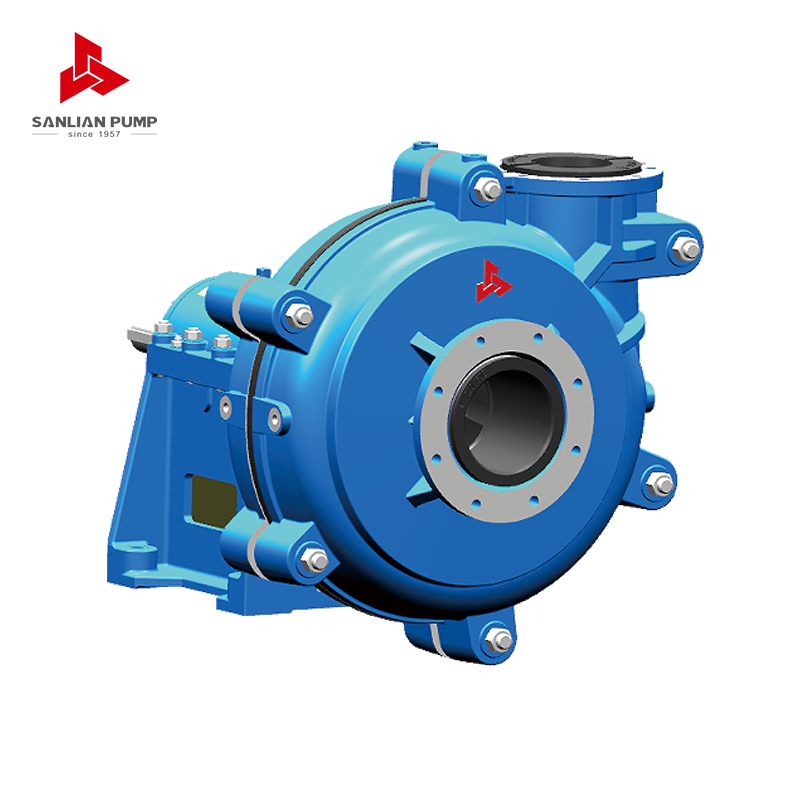
3. Vane Geometry and Thickness
The shape, number, and thickness of the impeller vanes influence how the slurry flows through the pump:
Thicker vanes provide added resistance to erosion and are typically used in heavy-duty slurry pumps.
Wide, open flow paths between vanes help reduce blockage and turbulence, which can accelerate wear.
Straight vanes are often used to minimize wear by reducing impingement angles, while curved vanes may improve hydraulic performance but can increase localized erosion if not properly designed.
4. Flow Characteristics and Efficiency
Efficient impeller design minimizes turbulence and ensures smooth, continuous flow of slurry. Turbulent flow not only reduces efficiency but also increases erosion by causing particles to impact surfaces at high velocity. A well-optimized impeller balances hydraulic performance with mechanical durability, ensuring that the pump operates efficiently over a longer period even in aggressive service conditions.
5. Impeller Clearance and Adjustability
Maintaining optimal clearance between the impeller and casing or liners is essential in slurry applications. Adjustable impeller designs allow for realignment as wear progresses, maintaining performance without frequent part replacements. This is especially important when dealing with abrasive slurries, where erosion of critical clearances can lead to reduced efficiency and higher energy consumption.
6. Cavitation Resistance
In applications with fluctuating pressure or flow conditions, impeller design must also consider cavitation resistance. Proper vane orientation and flow channel design can reduce the risk of vapor bubble formation and collapse, which can be highly destructive in slurry environments.
The impeller design in a slurry pump is a complex balance of material selection, hydraulic efficiency, solids handling capability, and wear resistance. Each design decision—whether it’s the type of impeller, its geometry, or the materials used—must be tailored to the specific characteristics of the slurry being pumped. For highly abrasive or corrosive applications, failure to optimize impeller design can lead to frequent downtime, increased maintenance costs, and reduced operational efficiency. Manufacturers like Sanlian Pump Group invest heavily in R&D to develop impeller designs that withstand harsh conditions while delivering consistent, long-term performance.