Maintaining efficiency across varying particle sizes and densities in slurry is a key design and operational challenge in slurry pump engineering. To address this, manufacturers and engineers incorporate several strategies into pump design and system integration. Here's a detailed explanation of how a slurry pump maintains efficiency under such variable conditions:
1. Optimized Hydraulic Design
Slurry pumps are engineered with specialized hydraulic geometries—particularly in the impeller and casing design—to ensure a smooth, non-turbulent flow even when the slurry contains a wide range of particle sizes. These features reduce energy losses caused by particle collisions and recirculation inside the pump.
Wide flow passages allow larger particles to pass through without clogging or disrupting the flow.
Reduced turbulence zones within the pump casing help maintain stable flow dynamics, minimizing hydraulic losses.
2. Impeller Design Tailored for Slurry Behavior
The impeller geometry—including the number, thickness, and shape of vanes—is crucial for managing variations in particle size and density.
Fewer, broader vanes provide better handling of coarse particles and prevent blockages.
Straight or slightly backward-curved vanes are often used to accommodate dense slurries with minimal internal pressure fluctuations.
Additionally, adjustable impeller clearances allow operators to compensate for wear and optimize performance over time, helping maintain efficiency even as operational conditions change.
3. Use of Wear-Resistant Materials
Efficient operation is closely tied to dimensional stability over time. In highly abrasive slurries, erosion can alter the internal profiles of flow paths, leading to reduced efficiency. By using high-wear-resistant materials—such as high-chrome alloys, rubber, polyurethane, or ceramics—the pump maintains its design tolerances longer, preserving its hydraulic efficiency.
4. Correct Pump Sizing and Operating Point
A properly selected slurry pump operates near its Best Efficiency Point (BEP). When pumping slurries with fluctuating solids content or densities, maintaining operation close to the BEP ensures that hydraulic losses are minimized.
Oversized pumps can experience low flow velocities, causing sedimentation.
Undersized pumps may struggle to maintain flow, leading to excessive wear and drop in efficiency.
By selecting a pump with a wide efficiency range, operators can accommodate variations in slurry composition without significant performance degradation.
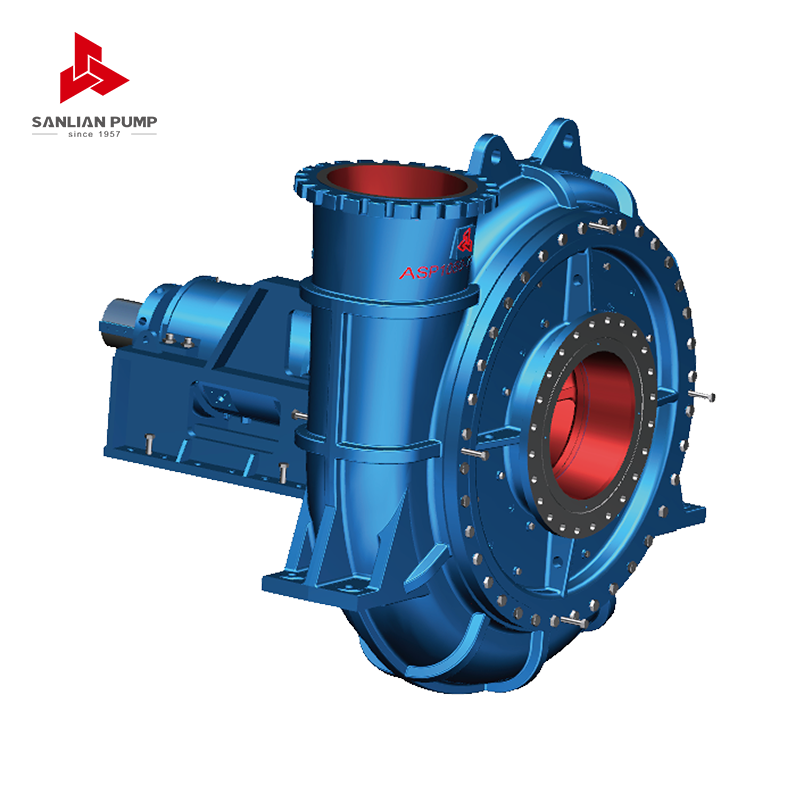
5. Variable Speed Drives (VSDs)
In systems where slurry density or particle concentration fluctuates significantly, using variable speed drives allows real-time adjustment of the pump speed. This helps maintain an optimal flow rate and head, improving both energy efficiency and system reliability.
For low-density slurries, reducing speed avoids excessive power consumption.
For high-density or larger particles, increasing speed can maintain sufficient velocity to prevent settling and blockages.
6. System Design Integration
The pump does not operate in isolation; system components such as piping layout, elevation, and valve configuration influence how efficiently the pump handles variable slurries.
Properly sized and aligned pipelines help prevent flow restrictions that could destabilize pump performance.
Use of agitation or recirculation loops can maintain homogeneous slurry consistency, improving pump efficiency.
7. Testing and Computational Modeling
Leading pump manufacturers like Sanlian Pump Group often use Computational Fluid Dynamics (CFD) simulations and real-world slurry testing to fine-tune their pump designs. This ensures the pump performs efficiently across a range of slurry types, from low-density wastewater to high-density tailings.