In the world of centrifugal pumping systems, efficiency and longevity are not mere aspirations—they are essential. At the heart of this pursuit lies a small yet critical component: the wear ring. Though often overlooked, wear rings serve a pivotal role in the performance and maintenance of split case pumps. Their presence is not optional—it is strategic.
The Anatomy of a Split Case Pump
Before exploring the function of wear rings, it’s important to understand the design of a split case pump. This pump configuration features a horizontally split casing, allowing for easy access to internal components without disturbing piping connections. Its robust construction and symmetrical layout make it ideal for high-flow, low-to-medium-head applications across industries.
But this design also presents a unique challenge: maintaining close tolerances between the impeller and the pump casing. That’s where wear rings come into play.
Defining the Purpose of Wear Rings
Wear rings act as sacrificial elements that preserve the critical clearance between the impeller and the casing. These precision-engineered rings are typically installed on both the impeller and the pump casing to form a narrow annular gap—minimizing internal leakage of fluid from the high-pressure side to the low-pressure side.
By limiting this recirculation, wear rings directly contribute to:
Improved Hydraulic Efficiency: Reduced fluid bypass enhances volumetric efficiency, maintaining optimal pump performance.
Component Preservation: Instead of eroding the costly impeller or casing, wear rings absorb wear from friction and particle abrasion—delaying the degradation of primary components.
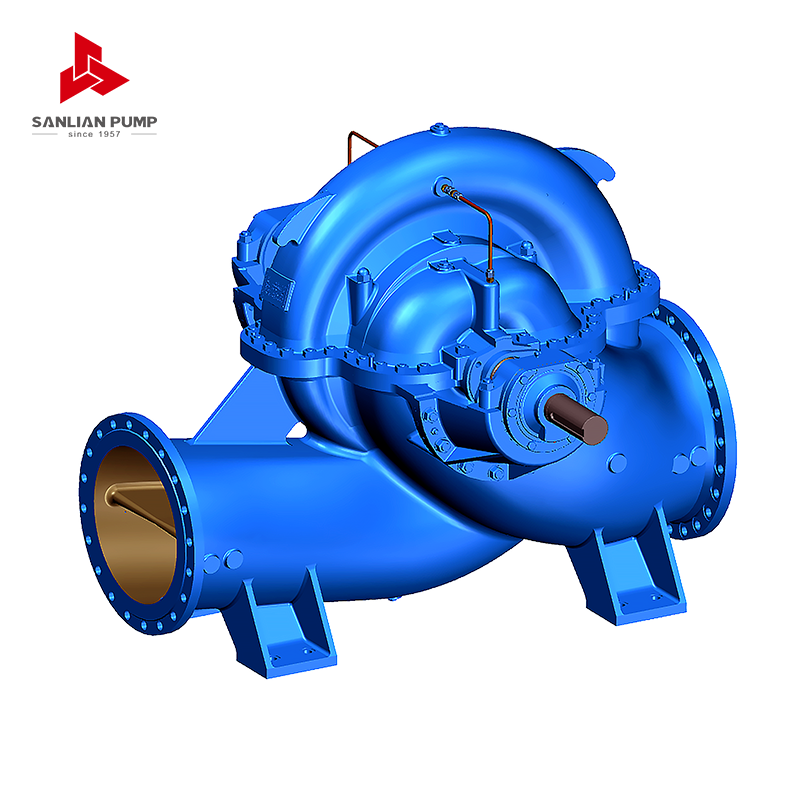
Cost-Effective Maintenance: Replacing wear rings is considerably less expensive than repairing or replacing an impeller or casing. Their modular nature simplifies routine overhauls and reduces downtime.
Material Matters
Wear rings are typically manufactured from materials selected for their wear resistance, such as bronze, stainless steel, or non-metallic composites. The pairing of ring materials is deliberate: one harder, one softer. This material differential helps control wear patterns and prevents galling under tight tolerances.
The Danger of Neglect
Operating a split case pump with worn or improperly fitted wear rings leads to increased internal leakage, eroded performance curves, and accelerated component fatigue. Over time, the cumulative effect of this inefficiency can ripple through an entire system—raising energy consumption, increasing maintenance frequency, and compromising system reliability.
In split case pump design, wear rings may be small, but their role is anything but minor. They guard against inefficiency, safeguard major components, and streamline maintenance operations. By maintaining tight internal clearances and mitigating hydraulic losses, wear rings serve as silent custodians of pump longevity.
Investing in quality wear rings—and replacing them at recommended intervals—is not just good practice. It is essential strategy.